Description
- 2-DOF PID algorithm optimized for various control applications
- 50ms high-speed sampling rate and ±0.2% display accuracy
- Program control and fixed control models available
– Up to 10 patterns x 20 steps program setting (program control model)
– Timer function for preset operation (fixed control model) - Simultaneous heating/cooling and automatic/manual control function
- Control functions: Group PID, Zone PID, Anti Reset Windup (ARW)
- Control status monitoring of up to 10 events
- RS485 communication output model available
– Communication protocols: Modbus RTU/ASCII, PLC ladder-less, Sync-Master
– Communication speed: up to 115,200bps - Heater burnout alarm function (CT input)
- Parameter setting via PC
– Comprehensive Device Management Software (DAQMaster) provided
– Communication converter connection with front loader port (TNH, TNL only) - Shortcut key setting with front user key button (U)
- Easy maintenance with detachable terminal blocks
![]() ![]() |
![]() ![]() |
![]() ![]() |
![]() ![]() |
![]() ![]() |
![]() ![]() |
![]() ![]() |
![]() ![]() |
![]() ![]() |
![]() ![]() |
2-DOF PID Control Optimized for Various Control Applications
The two-degree-of-freedom (2-DOF) algorithm can accurately reach the set temperature (SV) and respond quickly to disturbances for accurate and precise temperature control.
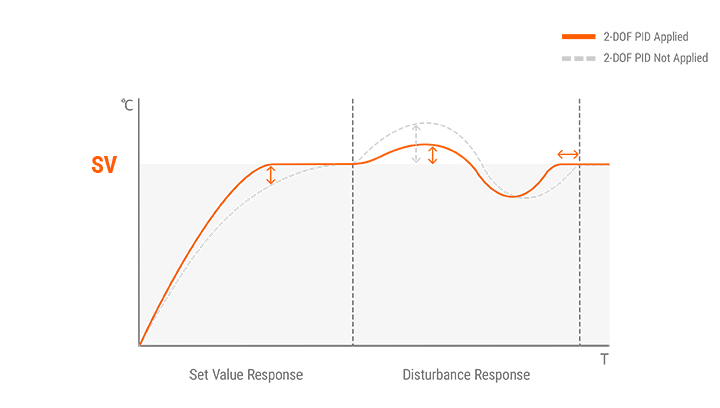
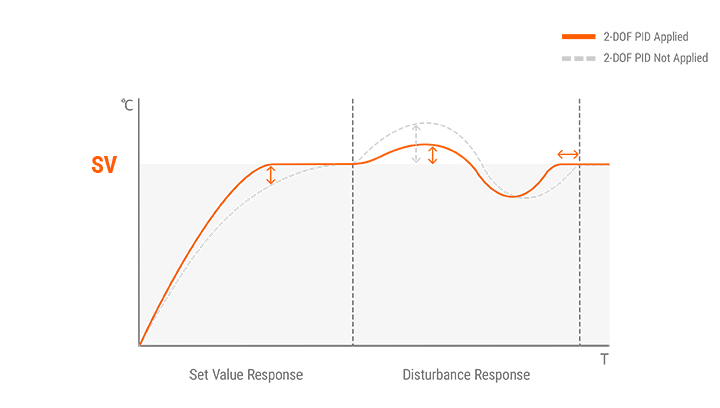
Program Control and Fixed Control Models Available
Users can choose between two model types for optimal control in various environments. Program control models offer pattern control with easy parameter settings and fixed control models offer timer function.
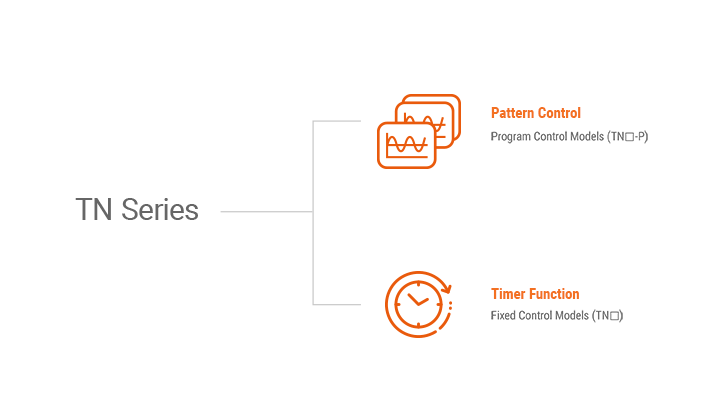
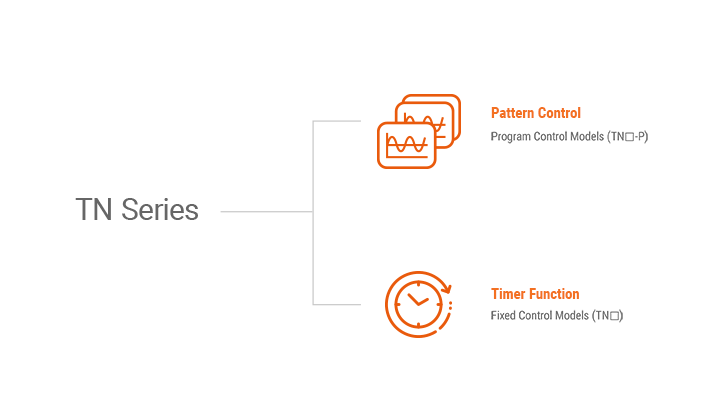
Easy Parameter Setting for Pattern Control (Program Control Models)
Program control models can be used to easily set the control pattern by sequentially setting the target temperature and time of each step. Users can easily draw the pattern with DAQMaster software by clicking the coordinates of the time-temperature graphs.
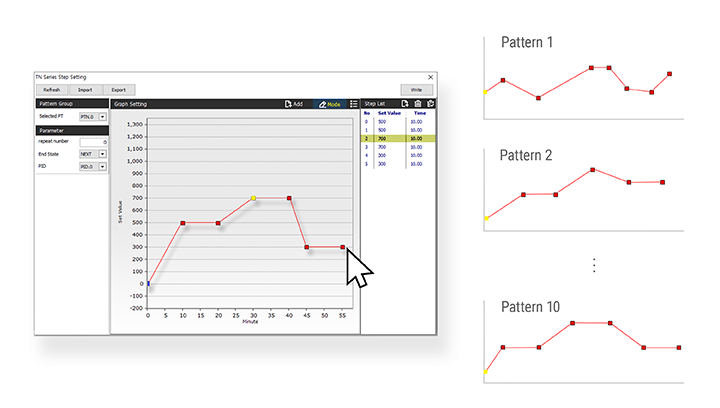
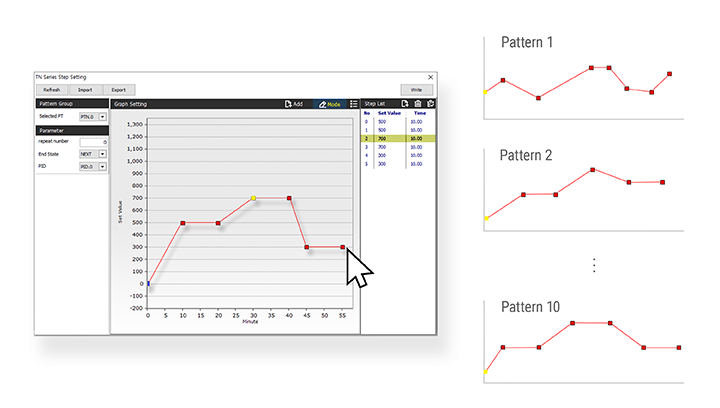
Timer Function for Preset Operation (Fixed Control Models)
Fixed control models can be used to preset the operation time by delaying the On/Off control outputs or by maintaining the PV for a set amount of time.
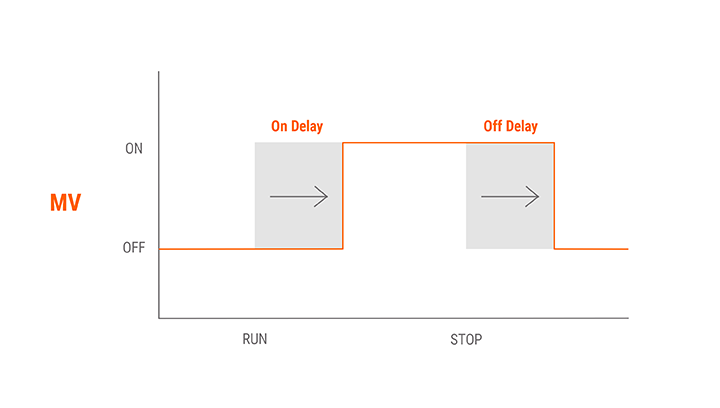
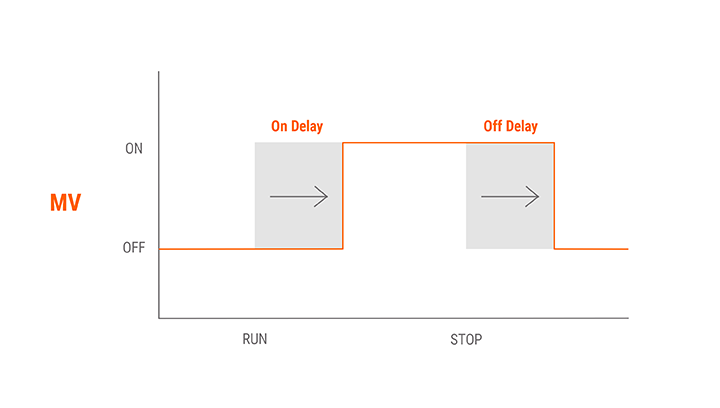
Various Control Function Supported
Various control function including Group PID, Zone PID, and Anti Reset Windup (ARW) available for optimal PID control in various environment.
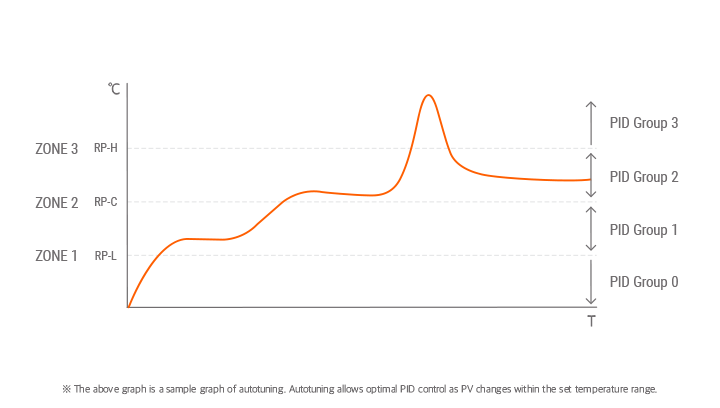
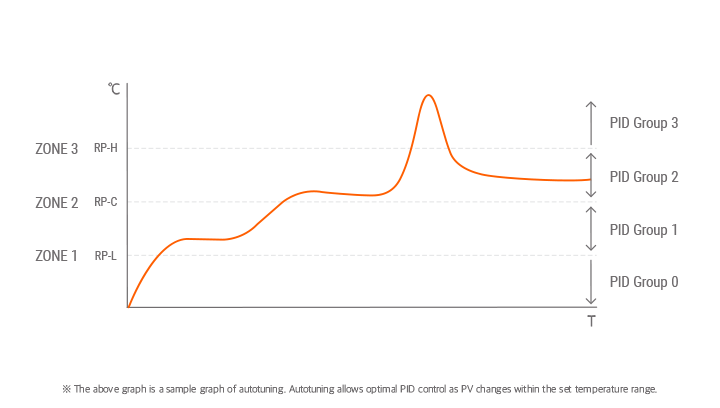
[Group PID and Zone PID Function]
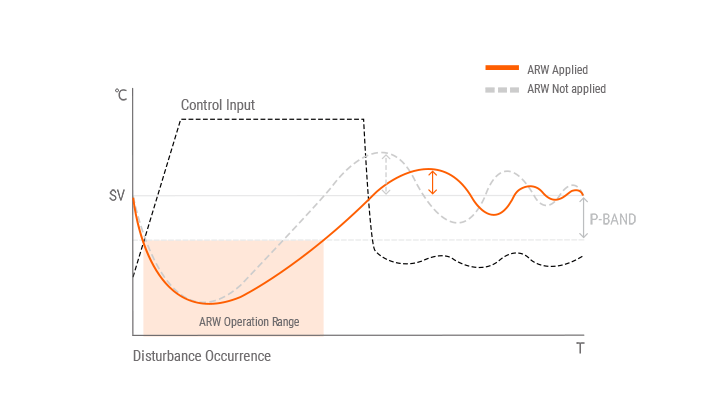
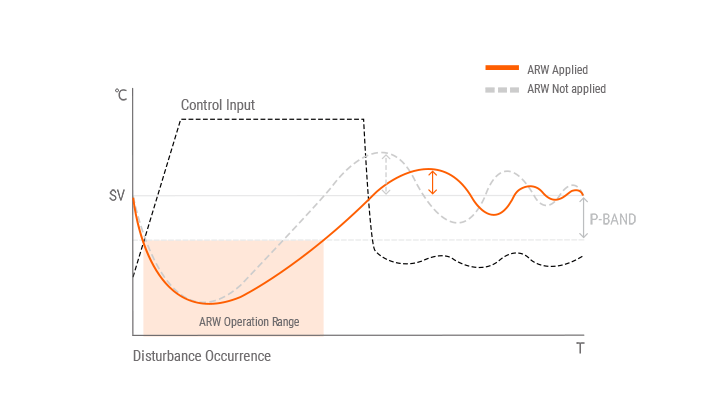
[Anti Reset Windup (ARW) Function]
When the control output reaches the maximum point, the range can be set to perform the integral operation to prevent overshoot with ARW function.
Control Status Monitoring of Up to 10 Events
Users can set up to 10 events such as PV high/low limit, disconnection and control operation notification. Logic operation result can be transmitted with relay alarm output and real-time monitoring is possible via RS485 communication.


SSR Drive Output Control Options
Users can select from ON/OFF control, cycle control, and phase control using standard SSR drive output option. Precise and accurate control is possible at low costs.
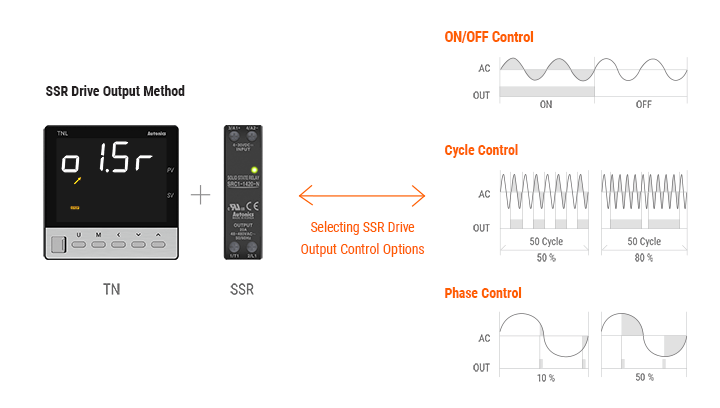
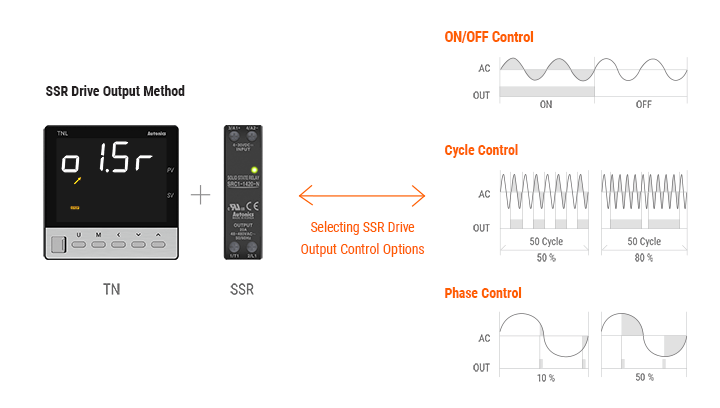
Easy Set up with PLC Ladder-less Communication
The controllers feature ladder-less and RS485 communication that can communicate with master devices (PLCs) without extra ladder programming.
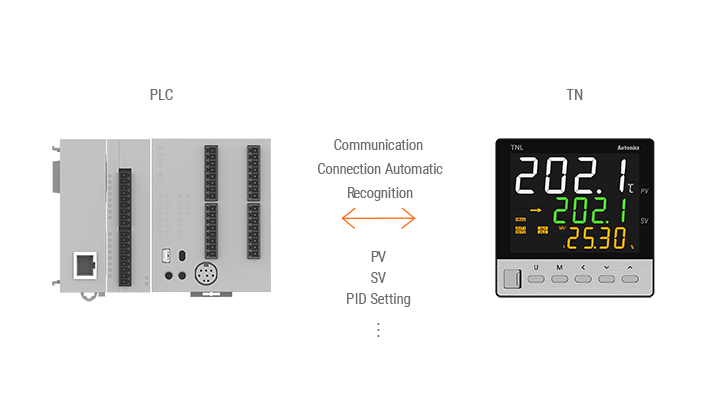
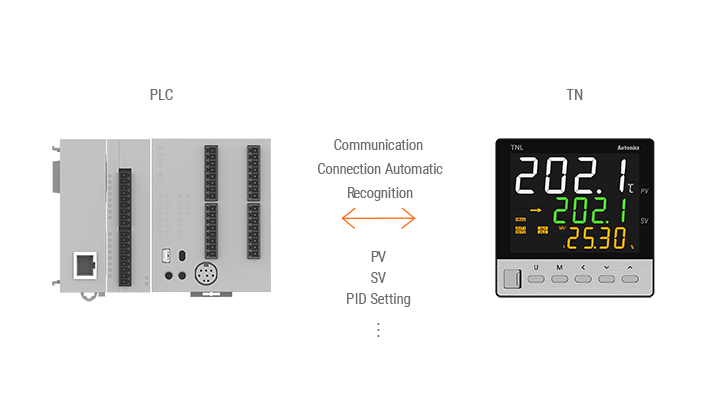
Synchronous Control with Sync-Master Communication
The SV and Run/Stop status of the master device can be synchronized with up to 31 slave devices to simultaneously control multiple zones.
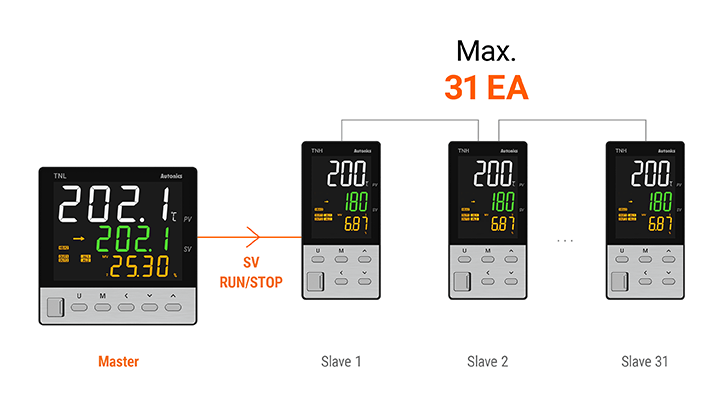
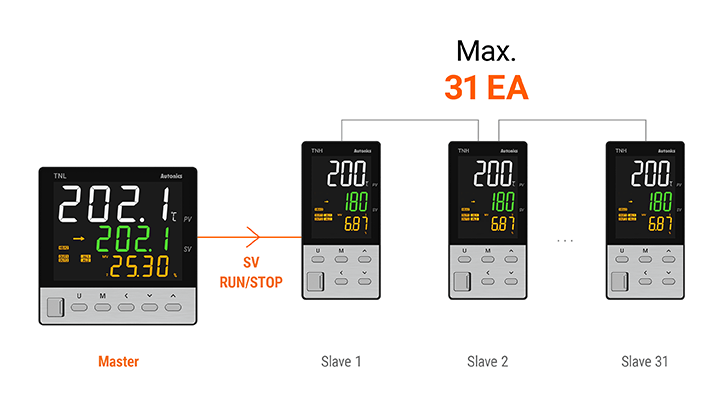
Applications
-
Electric Furnace
The set temperature (SV) and control status (Run/Stop) of multiple controllers can be synchronized in separated zones.
-
Raw Material Mixing Tank
Temperature controllers are used to control appropriate temperature and time for each raw material to equalize the production quality.
-
Sterilization Machine
Temperature controllers are used to control and maintain appropriate temperature for sterilization in machines.